Text: Detlev Herbst – Layout u. Gestaltung: Harald Wokittel
Die Glashütte Triebel in Triebel, Niederlausitz
Der Ursprung der Glashütte Buder liegt in Triebel, Niederlausitz, jenseits der Oberlausitzer Neiße im heutigen Polen. Zu den damaligen drei Eigentümern der Glashütte Triebel gehörte neben Werner Strietzel der Kaufmann Ernst Buder. Zusammen mit seiner Ehefrau Erna, geb. Strietzel, besaß er noch eine Kristallglasschleiferei in Krauschwitz, die seine Frau leitete.
In der Glashütte Triebel waren vor 1945 bis zu 300 Glasmacher mit der Herstellung von Hohl- und Kristallglas beschäftigt. Das Rohglas wurde anschließend in der hauseigenen Schleiferei in Krauschwitz veredelt. Die Familie Buder wohnte in Bad Muskau jenseits der Neisse. Beide Betriebe wurden nach 1945 enteignet.[1]
Die Suche nach einem neuen Standort in Westdeutschland
Seit Mitte 1947 berieten Mitglieder der Familie Buder darüber, eine neue Glashütte in Westdeutschland aufzubauen. Erna Buders Bruder Werner Strietzel lebte nach seiner Entlassung aus der Kriegsgefangenschaft in der britischen Besatzungszone. Ende 1947 nahm er auf der Suche nach einem geeigneten Grundstück Verbindung mit dem Wirtschaftsministerium in Hannover auf. Sein dortiger Gesprächspartner Dr. Hennecke verwaltete im Auftrag der britischen Militärregierung das Gelände der ehemaligen Heeresmunitionsanstalt Volpriehausen bis zur endgültigen Klärung, ob die Anlage gesprengt oder einer zivilen Nutzung zugeführt werden sollte. Bei einer Ortsbesichtigung erwies sich die Anlage als brauchbar für die Nutzung als Glasfabrik.
Im Juni 1948 beantragte Strietzel beim Niedersächsischen Wirtschaftsministerium in Hannover, das Gelände zur Nachnutzung freizugeben. Da sich zwischenzeitlich weitere Interessenten gemeldet hatten, zogen sich die Verhandlungen jedoch in die Länge.
Erst im Mai 1949 kam es schließlich zu den entscheidenden Gesprächen mit dem Wirtschaftsministerium und der Oberfinanzdirektion Hannover. Der Abtransport des Reparationsguts aus der früheren Heeresmunitionsanstalt durch die britischen Besatzungsbehörden war inzwischen abgeschlossen, so dass das Gelände dem ursprünglichen Besitzer, der Burbach Bergbau AG. zurückgegeben werden konnte. Ernst Buder, der im Herbst 1949 nach Volpriehausen gezogen war, konnte nun in Verhandlungen mit der Burbach Bergbau AG über die pachtweise Überlassung des Geländes und mit verschiedenen Banken zur Finanzierung des Vorhabens in Verhandlung treten und diese erfolgreich abschließen.[2]
Beginn der Produktion
Am 1. 10. 1949 begannen 15 Arbeiter aus der ehemaligen Glashütte Triebel, die mit Ernst Buder nach Volpriehausen übergesiedelt waren, mit den Aufräumung- und Instandsetzungsarbeiten in den Gebäuden. Nach deren Abschluss im August 1950 konnte die Produktion in bescheidenem Umfang in der früheren Kraftzentrale des Kaliwerks aufgenommen werden. Zur Verfügung standen dafür lediglich mehrere Maschinen und 13 Formensätze für Kristallglas, die die Familie aus Triebel mitgebracht hatte.[3] Sobald die benötigten Rohstoffe zur Verfügung standen, wurden nach und nach weitere Formensätze hergestellt. In der Anfangsphase wurde hauptsächlich mundgeblasenes und maschinell hergestelltes gepresstes Glas produziert, das in der eigenen Schleiferei handgeschliffen wurde. Den größten Anteil an der Produktion hatten jedoch dringend benötigte medizinische Gläser wie Apotheker- und Reagenzgläser, Medizinfläschchen, Nierenschalen und auch Akkumulatorengläser.
Schnell wuchs die Belegschaft auf 45 Mitarbeiter an, hauptsächlich erfahrene Glasmacher aus dem Sudetenland, Schlesien, Thüringen und der Niederlausitz. 1951 wurde der erste Betriebsrat gewählt. 75 % der Belegschaft waren gewerkschaftlich organisiert. Prokurist der Firma war Werner Strietzel.[4]
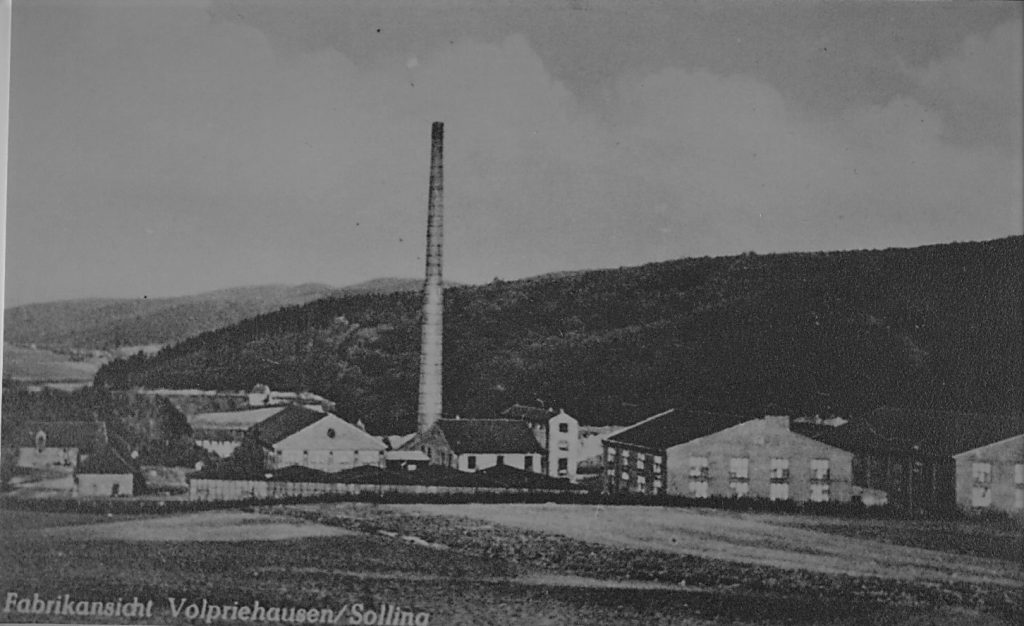
Der Zugang zum westdeutschen Markt war für die neugegründete Glashütte Buder schwierig, da die alteingesessenen westdeutschen Glashütten die Nachfrage im Inland bereits größtenteils abdeckten. Buder musste neue Absatzmärkte erschließen und produzierte für den Export – mit unerwartetem Erfolg. Bald gingen bis zu 75 % der Produktion in den Export in westeuropäische Länder, so dass die Anzahl der Beschäftigten in den Jahren 1952/ 53 auf 380 anstieg. Buder trug dadurch erheblich dazu bei, dringend benötigte Devisen für den Aufbau des Landes Niedersachsen zu beschaffen.[5] Der Versand der Bestellungen erfolgte als Expressgut vom Bahnhof Volpriehausen aus. Beinahe täglich wurden bis zu zehn Großaufträge in das In – und Ausland zum Versand gebracht.[6]
Der Herstellungsprozess von Kristall– u. Bleikristallglas
Glas ist eine aus verschiedenen Rohstoffen zusammengeschmolzene klare, gestaltlose, erstarrte, homogene, spröde Masse. Zur Herstellung von Kristallglas und Bleikristallglas verwendete die Glashütte Buder folgende Rezepturen:
Zutaten | Kristallglas | Bleikristallglas |
Quarzsand | 75 | 100 |
Soda | 17 | 5 |
Kalksteinmehl | 10 | 3 |
Pottasche | 8,5 | 26 |
Salpeter | 4,5 | 7 |
Baryt | 3 | 3 |
Arsen | 0,5 | 1 |
Mennige | 0 | 47 |
Borax | 1 | 4 |
Die Pottasche sorgt für einen besseren Glanz, Salpeter ist ein Läuterungsmittel für blasenfreies Glas, Arsen ist ein Läuterungsmittel für eine blasenfreie Glasmasse und Mennige erhöht die Brillanz.
Als Färbungsmittel wurden Kobaltoxyd (blau), Selenoxyd (rosa, rot) und Manganoxyd (violett) in Pulverform dem Gemenge beigefügt. [7]
Die Rohstoffe wurden genau abgewogen und in einer Maschine gemischt. Dem Gemenge wurden etwa 30 % aus der Produktion anfallende zerkleinerte Scherben beigemischt.
Die Glasherstellung erfolgte anfangs in Hafenöfen, die aus feuerfesten Steinen erbaut waren. Darin befanden sich mehrere Glasschmelzhäfen, in denen das Glas geschmolzen wurde. Sie waren normalerweise 655 cm hoch und 100 cm breit. Vor Gebrauch wurden die Steine mit Butangas auf 1200 – 1400 Grad erhitzt. Bis 1970 erzeugte die Glashütte Buder das Gas selbst. Die Glasschmelztemperatur liegt bei 1500 Grad. Wenn nach elf Stunden das Glas klar und blasenfrei war, wurde die Arbeitstemperatur auf 1150 Grad zurückgefahren. Die Häfen mussten durchschnittlich alle 14 Wochen erneuert werden. Dafür waren 17 Mitarbeiter nötig. Mit Hafenschmelzöfen konnte man nur periodisch arbeiten, konnte aber nach Bedarf verschiedene Glassorten schmelzen.
Die später benutzten Wannenöfen bestanden aus einem großen Schmelzbecken mit einem Fassungsvermögen von bis zu 100 t Glas. Das Rohstoffgemenge wurde aus einem Silo neben dem Ofen über eine Auslaufrinne kontinuierlich in die Schmelzwanne geschoben. Nachdem das Glas bei gleichbleibender Temperatur geschmolzen war, wurde es mechanisch vorne aus der Wanne gezogen, während hinten mit Hilfe eines Glasstandreglers die Rohstoffe kontinuierlich nachgeführt wurden. Die Glasqualität war bei Wannenöfen allerdings nicht so gut wie bei Hafenöfen. Diese konnten aber wirtschaftlicher in bis zu drei Schichten eingesetzt werden.[8]
Hohlglas:
Zur manuellen Herstellung von Glas benötigt man ein „Anfangeisen“, ein Stahlrohr von ca. 1,80 m Länge mit einem Holzgriff an einem Ende. Am anderen Ende befindet sich eine Hohlkugel, auf die das Glas durch Drehen „aufgewickelt“ wird. Der Durchmesser der Kugel variiert, so dass man unterschiedliche Mengen an Glas aufnehmen kann. Weiterhin benötigt man einen Wulgerlöffel und eine Form, in die das Glas eingeblasen wird. Der Wulgerlöffel ist ein vierkantiges Hartholz mit einer runden Vertiefung, in der das Glas gedreht wird. Die Formen sind aus Hartholz, Kohle oder Guss.[9]
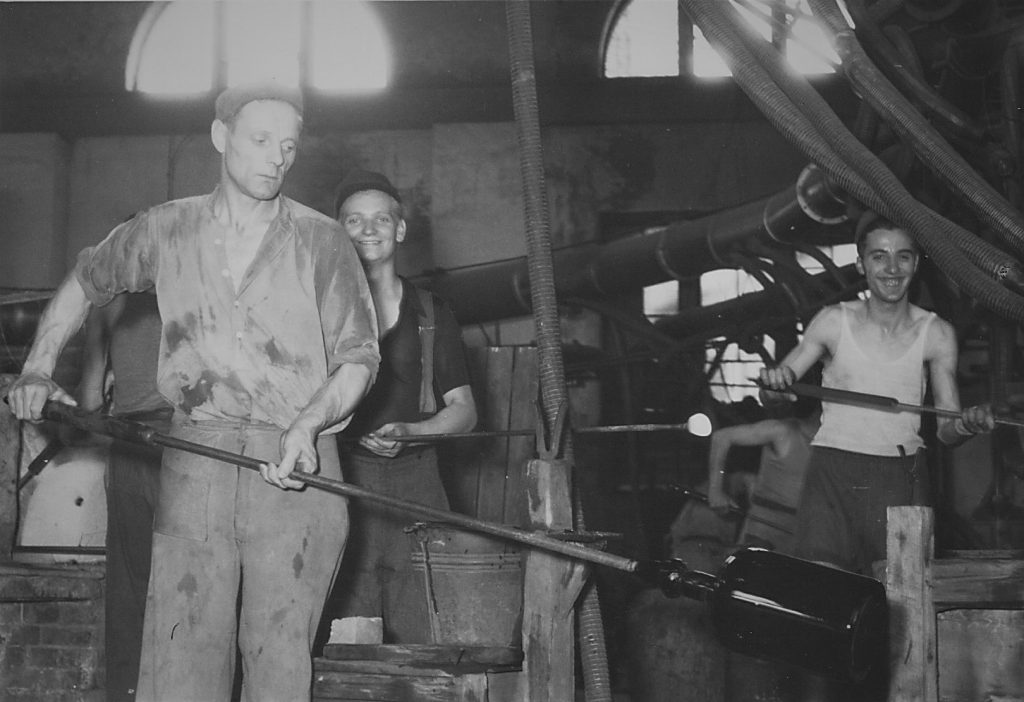
Der Glasmacher sticht mit der Pfeife in die Glasmasse und dreht sich die gewünschte Menge auf den Pfeifenkopf, wulgert das Glas durch ständiges Drehen im Holzlöffel zusammen. Die Glasmasse wird dann mit dem Holzlöffel vorgeformt, bevor die glühende Masse in die Form gebracht wird. Durch ständiges Drehen und Blasen wird die Wandung in der Form ausgeblasen. Das muss schnell vor sich gehen, damit das Glas nicht abkühlt. Ist das Glas fertig geblasen, wird die Form geöffnet und der Glasmacher nimmt das fertige Stück mit der Pfeife aus der Form. Das Glasstück wird anschließend mit einem Schlag auf die Pfeife von ihr getrennt und kommt zur Kühlung auf das Kühlband.[10]
Pressglas:
Der Glasanfänger holt das Glas aus dem Ofen und lässt es in die bereitstehende heiße Metallform laufen. Der Presser schneidet das laufende Glas mit einer Schere ab und schiebt die Form unter die Presse. Mit einem Hebeldruck drückt die Glaspresse den Stempel in die glühende Glasmasse und das Glas an die Wandung der Form. Der Stempel löst sich wieder und das erstarrte Glas kann der Form entnommen werden. Die Pressformen bestehen aus einer speziellen hitzebeständigen Gusslegierung. In den Formen sind bereits die Muster und Verzierungen eingearbeitet, die beim Hohlglas erst eingeschliffen werden.
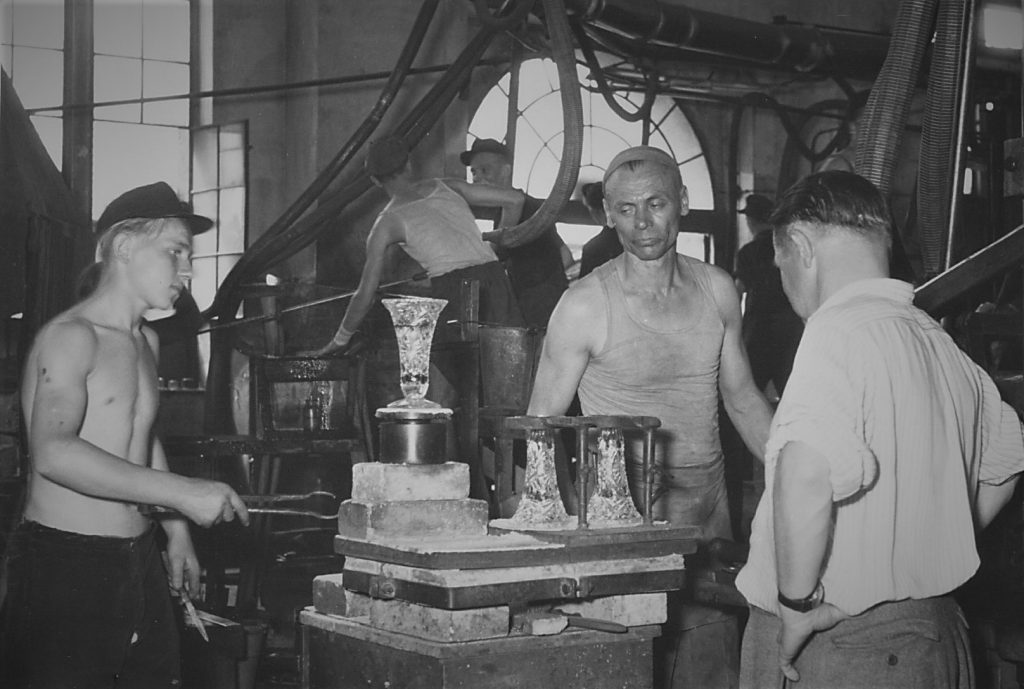
Die schnelle Abkühlung des Glases von 1150 auf 550 Grad kann zum Bruch führen. Um solche Zug- und Druckspannungen zu verhindern, durchläuft das Glas auf einem durchgehenden Drahtgitterförderband ein Kühlbad. Bei der langsam sinkenden Temperatur von 540 Grad beträgt die Abkühlzeit bei Kristallglas ungefähr 2 – 3 Stunden.
Um dem Bleikristallglas seine typische Brillanz zu geben, wird es in einem Bad aus Fluss- und Schwefelsäure säurepoliert. [11]
Die goldenen sechziger Jahre
Die gute wirtschaftliche Entwicklung hielt auch in den folgenden Jahren an, so dass 1955 ein zweiter Ofen für gepresstes und mundgeblasenes Bleikristall in Betrieb genommen werden konnte. Dieser wurde im Gegensatz zum ersten Ofen, der „Ersten Hütte Müßig“ als „Zweite Hütte Buder“ bezeichnet.

Die Abteilung für medizinische Gläser wurde Ende der fünfziger Jahre aus Rentabilitätsgründen stillgelegt. Die hundert Mitarbeiter der Abteilung wurden auf andere Bereiche verteilt.
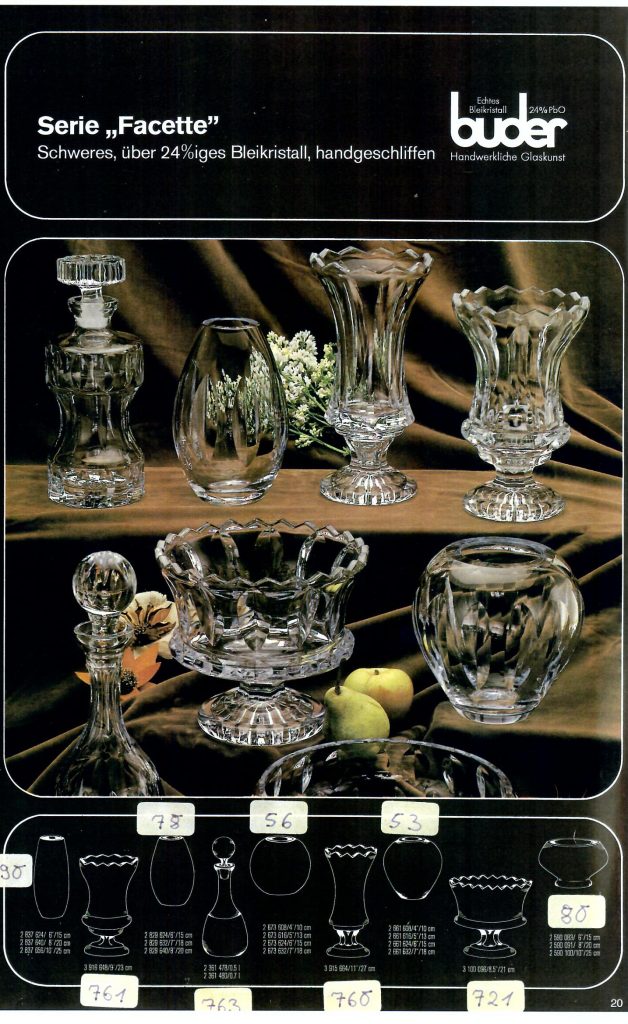
Durch die Gründung der Glashütte und die gute Sozialpolitik des Betriebes gelang es Buder, viele Vertriebene im Dorf sesshaft zu machen, da er ihnen neben einem guten Arbeitsplatz auch ansprechende soziale Rahmenbedingungen bieten konnte. Er führte eine Betriebsrente für alle Mitarbeiter ein und gewährte Privatkredite zu sehr günstigen Konditionen. In der Schachtstraße ließ er für seine Mitarbeiter sechs Mehrfamilienhäuser mit günstigen Werkswohnungen errichten. Im Betrieb wurden eine Kantine, die auch für private Feiern nutzbar war, und eine Kegelbahn gebaut. Die Kantine war der gesellschaftliche Mittelpunkt des Betriebs, ohne zu übertreiben kann man sagen des Dorfs. Sie war der Treffpunkt für Skatspieler und Knobler, vom Mitarbeiter bis zum Chef. Es gab darüber hinaus einen Fernsehraum, Tischtennisplatten, einen Tennisplatz und eine betriebseigene Fußballmannschaft. Die Faschingsfeste in der Hütte waren legendär und sind noch heute zahlreichen Dorfbewohnern in guter Erinnerung. [12]
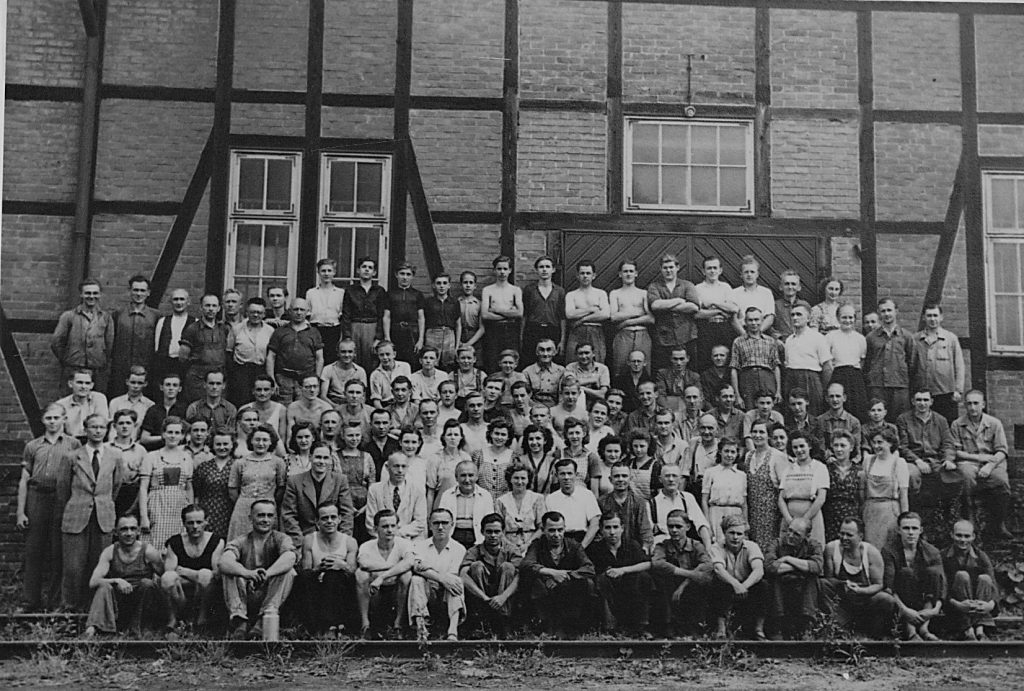
Immer wieder kam es auf dem Werksgelände zu schweren Betriebsunfällen, die wegen großer Schäden zeitweise sogar zu Produktionsunterbrechungen führten. Mitte Mai 1963 brannte das Kühlband, das die Hütte mit der Schleiferei verband. Dabei wurden auch der Dachstuhl der Schleiferei und die Lagerräume für Rohfertigprodukte und Packmaterial schwer beschädigt.
Es entstand ein Sachschaden in Höhe von 1 Million DM. [13]
Infolge eines Defekts am Füllstandsanzeiger des Schwefelsäuretanks liefen im August 1968 6000 Liter 98 prozentige Schwefelsäure aus. Sie gelangten über den Rehbach, die Ahle und Schwülme bis in die Weser und verursachten ein großes Fischsterben.
Nach längeren Verhandlungen mit der Burbach Bergbau AG hatte die Glashütte das Betriebsgelände mit allen Gebäuden 1966 kaufen können. Der Tod des Firmengründers Ernst Buder 1969 bedeutete einen großen Einschnitt in der Firmengeschichte. Seine drei Söhne Rainer, Ulrich und Dieter traten die Nachfolge an, Rainer Buder übernahm die Betriebsleitung, Ernst Buders Witwe Erna die Geschäftsführung. [14]
In den Jahren bis 1969 lief die Produktion auf Hochtouren. Der Absatz war dank steigender Nachfrage und entsprechender Gewinne gut, das Steueraufkommen entsprechend. Die Mitarbeiterzahl stabilisierte sich bei 300, der Exportanteil lag bei etwa 25 %. In der Schweiz, in Italien und den Niederlanden, die zu den größten Abnehmern gehörten, waren eigene Auslandsvertreter tätig.
In dieser Blütezeit wurde allerdings versäumt, die Gebäude und Produktionsmittel zu erneuern und die Forschung und Entwicklung neuer Produkte und Produktionsmethoden voranzutreiben.
Absatzkrise und erster Konkurs
Anfang der siebziger Jahre zeichnete sich ein Rückgang des Umsatzes ab. Bereits 1971 musste Rainer Buder die Belegschaft darüber informieren, dass die Glashütte im Vorjahr erstmals rote Zahlen geschrieben hatte. Diese Entwicklung hing nicht nur mit veränderten Marktbedingungen und der starken osteuropäischen Konkurrenz, vor allem der Tschechoslowakei, zusammen. Der Krankenstand im Betrieb war hoch, das Betriebsklima hatte sich erheblich verschlechtert. Trotz der rückläufigen Produktion wurden im Juli 1972 die Löhne um 7 %, das Weihnachtsgeld von 70 auf 85 % erhöht. Die Löhne lagen dank eines Hausvertrags über denen des gültigen Tarifvertrags. Hinzu kam, dass der Landkreis Northeim aus Gründen des Umweltschutzes die Auflagen für die weitere Produktion verschärfte.
Infolge der sich abzeichnenden Rezession wurden im Januar 1973 der Ofen 3 stillgelegt und 30 Mitarbeiter entlassen. Ein weiterer Schmelzofen war ausgefallen und musste dringend repariert werden. Die Belegschaft hatte sich dadurch auf 252 Beschäftigte verringert. Im März 1973 kürzte die Shell AG schließlich die Butangaslieferungen. Der Lagerbestand an unverkauften Glaswaren wuchs stetig. Um ihn nicht noch weiter anwachsen zu lassen, beschloss man, die Verkaufspreise zu senken.
Trotz der sich verschlechternden wirtschaftlichen Lage erzielte die Glashütte 1973 noch einen Umsatz von 7 Millionen DM. [15]
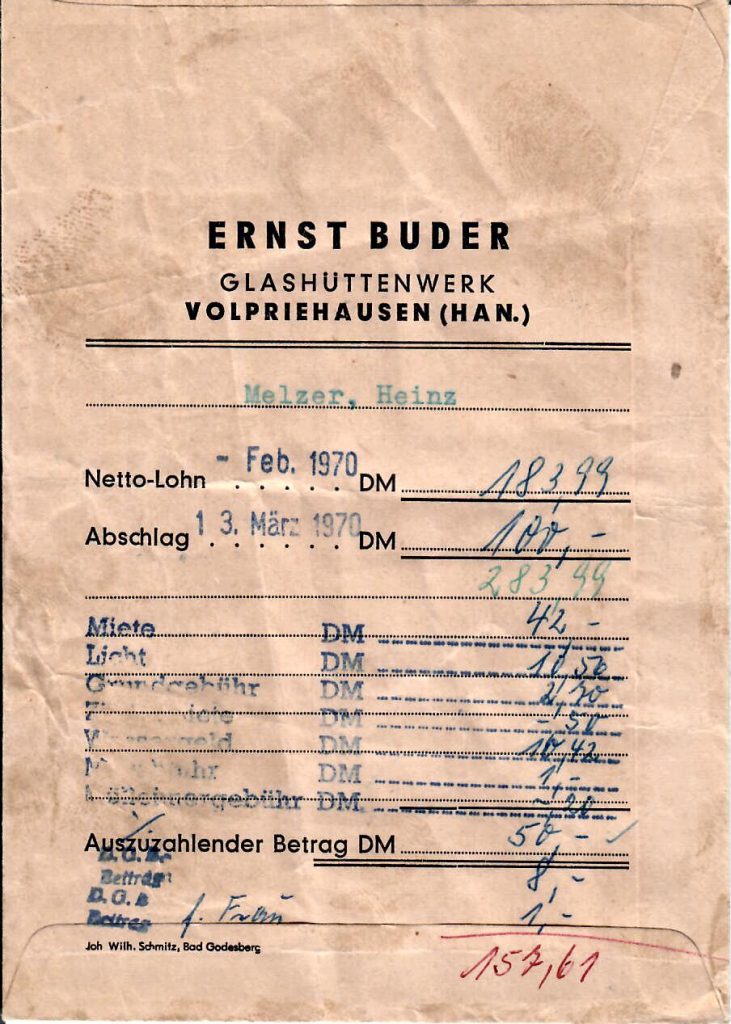
Am 19. 8. 1974 meldete die Glashütte beim Amtsgericht Northeim Konkurs wegen fehlender liquider Mittel an. Das Land Niedersachsen hatte eine Bürgschaft für weitere Kredite abgelehnt. Dadurch waren die Arbeitsplätze von 240 Mitarbeitern gefährdet.[16]
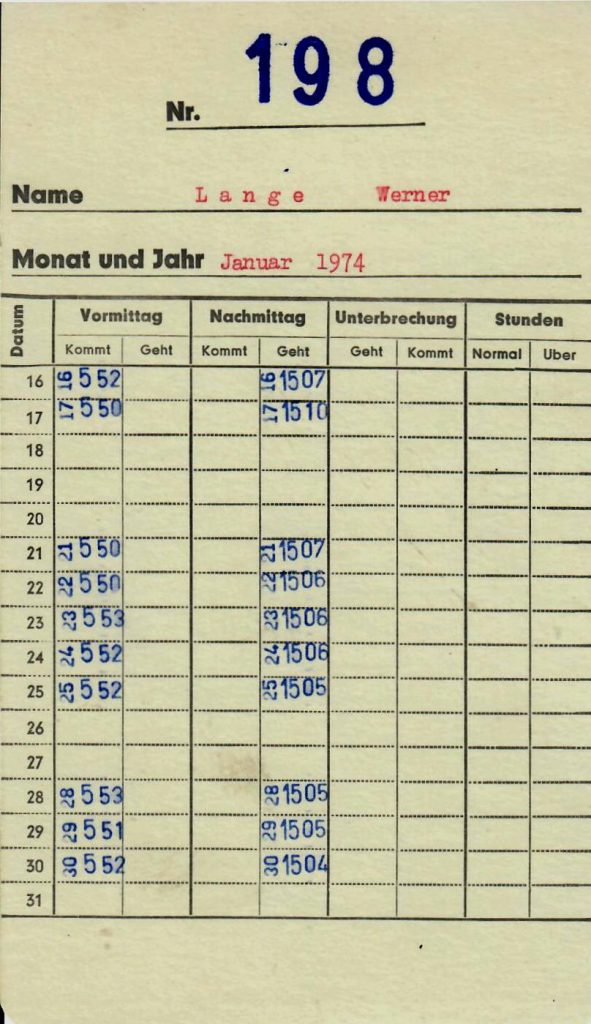
Um diese noch zu retten, schlug der Konkursverwalter die Gründung einer Auffanggesellschaft vor. Geschäftsführer sollte ein Unternehmensberater aus Stuttgart werden. Bei den Verhandlungen zur Gründung der Auffanggesellschaft stellte sich heraus, dass für den Neustart ein Eigenkapital von nicht weniger als 2 000 000 DM benötigt würde.
Neugründung der Kristallglaswerk Buder GmbH + Co KG
Nach langwierigen Verhandlungen mit den Gläubigern und potentiellen Geldgebern konnten die ehemaligen Geschäftsführer Werner Strietzel und Herbert Rückert im Dezember 1974 mit einem Eigenkapital von 700 000 DM und einem Investitionskredit in Höhe von 1, 7 Millionen DM die Voraussetzungen für einen Neustart schaffen. Das Land Niedersachsen bürgte für den Investitionskredit, die Kreditgeber waren die Norddeutsche Landesbank, die Deutsche Bank Göttingen und die Volksbank Volpriehausen. Weitere 1 000 000 DM in Form eines Betriebsmittelkredits stellten Vertreter, Lieferanten, Mitarbeiter und ortsansässige Interessenten zur Verfügung.
Als Kontrollinstanz wurde ein Beirat gebildet, einem Aufsichtsrat vergleichbar, der aus einem Vertreter der kreditgebenden Banken, der Kommanditisten und der Arbeitnehmer bestand..
Am 9. Dezember 1974 nahm die Kristallglaswerk Buder GmbH + Co KG die Produktion auf ihrem alten, jetzt aber gepachteten Betriebsgelände wieder auf. Neben der Klärung der finanziellen Verhältnisse war der Rückkauf der Formen für die Glasherstellung vom Konkursverwalter Dr. Hahn in Wiensen eine weitere wichtige Voraussetzung für die Wiederaufnahme der Produktion.
Bei Produktionsbeginn bestand die Belegschaft aus etwa 90 Mitarbeitern, die alle schon in der Vorgängergesellschaft tätig gewesen waren. Nach der Fertigstellung der zweiten Ofenanlage Mitte Januar 1975 konnte die Belegschaft auf etwa 145 Mitarbeiter aufgestockt werden. Ziel war weiterhin, wieder die alte Belegschaftsstärke von 180 bis 200 Mitarbeitern zu erreichen. Dabei sollte auch die Schaffung von Ausbildungsplätzen für Jugendliche zu Glasmachern, Ziseleuren und Schleifern helfen. Als weitere Konsolidierungsmaßnahme folgte eine Sortimentsbereinigung. Es sollte überwiegend nur noch handgeschliffenes Bleikristall in gepresster Form hergestellt werden. Die Auftragslage entwickelte sich gut, die Hälfte der Produktion ging in den Export. [17]

1977 erfolgte die Umstellung auf den damals modernsten Wannenofen, einen sog. Bohemia-Melter, eine vollautomatische Schmelzwanne. Es handelte sich dabei um eine Neuentwicklung der tschechischen Glasindustrie, Der Melter wurde für Buder von einer deutschen Firma in Lizenz hergestellt und war der erste Wannenofen in Westeuropa überhaupt. Damit konnte man den Zweischichtenbetrieb als Regelarbeitszeit einführen und die wachsende Nachfrage nach Bleikristallglas preisgünstiger befriedigen. Seine Tagesleistung im Zweischichtensystem betrug kontinuierlich 6, 5 t Rohglas, das sofort weiterverarbeitet werden konnte. Die Kosten für die Anschaffung des Melters in Höhe von 850 000 DM konnten bei dem damaligen Jahresumsatz von 9 000 000 DM der Firma nur durch eine weitere Landesbürgschaft unter Beteiligung der Gesellschafter aufgebracht werden.[18]
Die beiden alten Hafenöfen wurden ausgebaut, da mit ihnen nur eine Produktionszeit von acht Stunden im Einschichtbetrieb möglich war. Mit der Anschaffung des Melters hoffte man, dem Wettbewerbsdruck der osteuropäischen Glashütten besser begegnen zu können. [19]
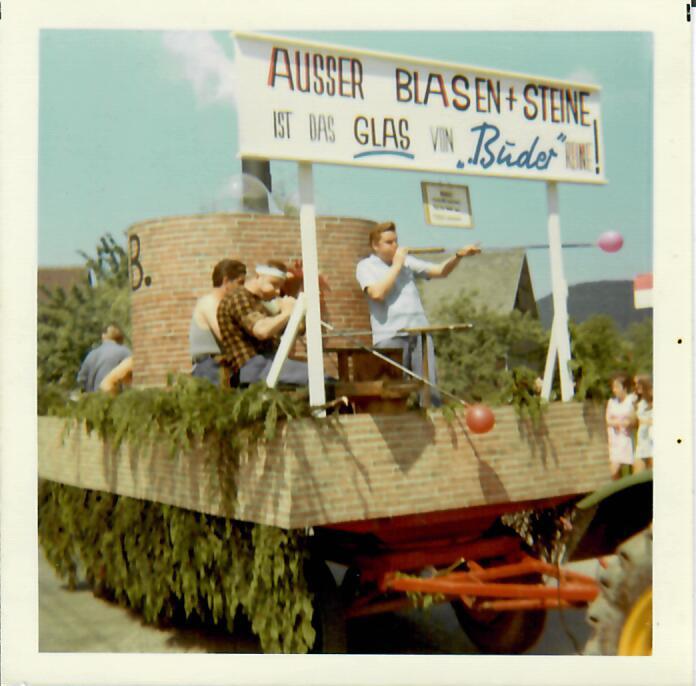
Die wachsende Nachfrage nach exklusiveren Produkten führte zur Einrichtung einer Veredlungsabteilung mit 40 Beschäftigten. Dort wurden Spezialaufträge wie Tiefschliff, Flächenschliff, Satinier- und Veredelung mit Gold und Lüsterfarben in Handarbeit ausgeführt. Alle Artikel wurden in der angeschlossenen Ätzerei hochglanzsäurepoliert. In größerem Umfang wurde auch wieder mundgeblasenes Glas hergestellt. Seit 1983 setzte die Glashütte einen modernen Kugelspeiser mit einem Mehrstationen-Pressautomaten ein.

Das Produktionsprogramm umfasste zu dieser Zeit einschließlich der Exklusivserien etwa 3000 Artikel, von denen 700 im aktuellen Programm für „den gedeckten Tisch“ und als Geschenkartikel erhältlich waren. 80% der Produktion waren maschinell hergestelltes Pressglas, und 20% mundgeblasenes Bleikristallglas.
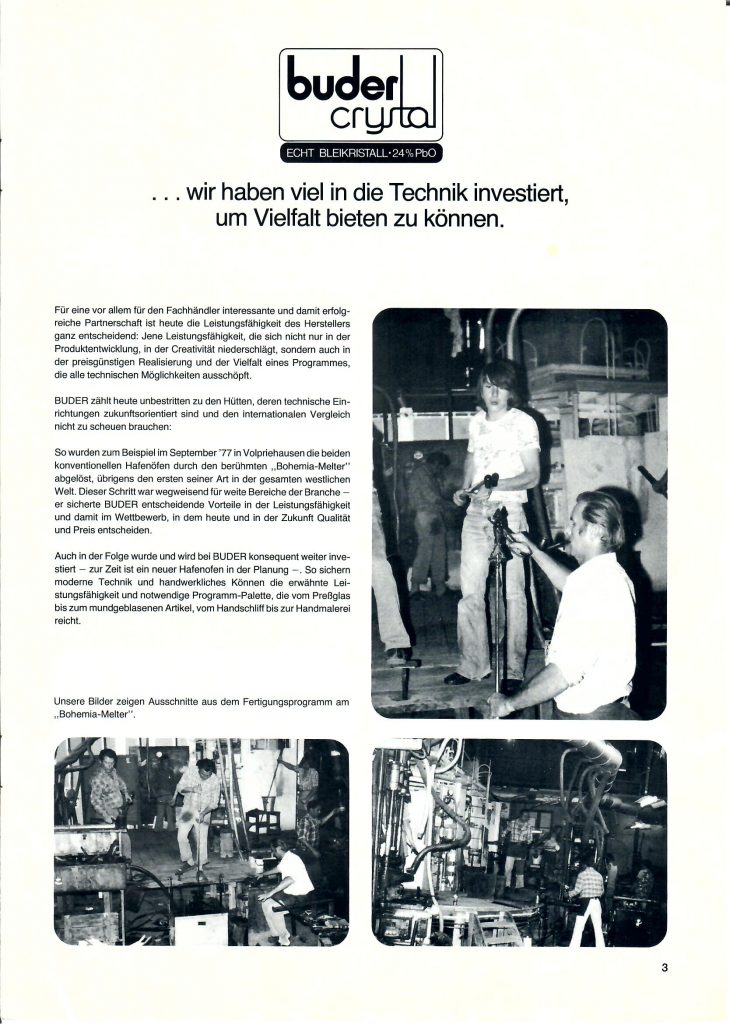
Der Vertrieb erfolgte über den Großhandel, Kaufhauskonzerne, Einkaufsgemeinschaften, Metallwarenfabriken und Exklusivkunden. Bis zu 70 % der Produktion wurden in westeuropäische Länder und nach Übersee exportiert. Außendienstmitarbeiter der Glashütte waren in allen westeuropäischen Ländern, den USA, Kanada und in mehreren arabischen und südamerikanischen Ländern tätig. [20] Die Mitarbeiterzahl hatte wieder 200 erreicht. [21]
Marode Betriebsanlagen und Entsorgungsprobleme
Trotz der erfreulichen Absatzentwicklung Anfang der achtziger Jahre kam es infolge des schlechten Zustands der Gebäude und technischen Anlagen immer wieder zu Betriebsunfällen, die neben hohen Sachschäden auch zu Unterbrechungen der Produktion führten.

Bei Wartungsarbeiten an der Gaszufuhr eines Brennofens kam es Mitte Juli 1983 zu einem Brand, der eine Formpresse und die dazugehörige elektrische Einrichtung schwer beschädigte. Ca 20 t Bleikristall wurden unbrauchbar. Es entstand ein Gesamtschaden von 250 000 DM. Die Produktion musste für zwei Tage unterbrochen werden. Anfang Dezember des gleichen Jahres kam es zu einem weiteren Zwischenfall, bei dem 2, 5 t flüssiges Glas aus einem Loch in der gemauerten Glasschmelzwanne ausliefen. Mehrere Tage Produktionsausfall waren die Folge. [22]
Hinzu kam, dass das Problem der Beseitigung und Lagerung der Produktionsrückstände nur unzureichend gelöst war. Die Entsorgung von Flusssäure, Schwefelsäure, Arsen und Blei enthaltenden Schlämmen wurde in sieben genehmigten Schluckbrunnen auf dem Werksgelände und außerhalb vorgenommen, führte aber immer mehr zu starken Belastungen der Umwelt.
Das niedrige Eigenkapital in Höhe von 900 000 DM und die sich bald wieder abzeichnenden Verluste ließen eine dringend erforderliche Modernisierung, Forschung und Entwicklung sowie Werbung nicht zu. Das Unternehmen sollte mit dem Ziel weitergeführt werden, unbedingt den Betrieb zu erhalten, da in der strukturschwachen Sollingregion arbeitslose Glasmacher keine Perspektive haben und wohl nur in Bayern einen neuen Arbeitsplatz finden würden. [23]
Schon im zweiten Quartal 1983 zeichnete sich wieder ein drohender Konkurs ab. Die Norddeutsche Landesbank, die Kreissparkasse Northeim und die Betriebsleitung der Glashütte beauftragten eine Hamburger Unternehmensberatung mit der Entwicklung eines nachhaltigen Sanierungskonzeptes für die Glashütte.
Das Gutachten, das im August 1983 vorgelegt wurde, forderte einschneidende Maßnahmen, um die Arbeitsplätze in der Glashütte erhalten zu können. Einvernehmlich wurde zügig mit der Umsetzung der geforderten Maßnahmen begonnen:
Im Spätsommer erfolgte der Austritt aus dem Arbeitgeberverband der Glasindustrie, um die hohen Mitgliedsbeiträge einzusparen. Bis Anfang 1984 wurde die Belegschaft um 50 Mitarbeiter reduziert. Lohnkürzungen um 20 % und die Aussetzung des Weihnachts- und Urlaubsgeldes traten ebenso ab 1984 in Kraft. Das bestehende Akkordsystem wurde abgeschafft. Die ausstehenden Löhne sollten ratenweise nachgezahlt werden.[24]
Auch die Stadt Uslar beteiligte sich an den Sanierungsmaßnahmen, indem sie im September 1984 für 350 000 DM mehrere bebaute und unbebaute Grundstücke der Firma Buder kaufte. Kurz darauf wurde bekannt, dass das Land Niedersachsen und die Stadt Uslar für zwei Millionen DM eine neue Kläranlage bauen wollten, um die weitere Verschmutzung des Rehbachs durch die Abwässer der Glashütte zu unterbinden, die giftige Säuren, Salze und Schwermetalle enthielten.[25]
Die eingeleiteten Maßnahmen führten jedoch nur zu einer kurzfristigen Entspannung der Lage, obwohl für 1974 sogar wieder ein geringer Betriebsgewinn zu verzeichnen war.[26] Sie kamen zu spät und berücksichtigten immer noch nicht ausreichend die Aspekte einer nachhaltigen umweltverträglichen Sanierung der Produktionsanlagen.
Erneuter Konkurs im November 1986
Am 10. 11. 1986 meldete die Glashütte Buder Konkurs beim Amtsgericht Northeim wegen fehlender Zahlungsbereitschaft an. Die Gründe für den erneuten Konkurs waren die vollkommen überalterten Produktionsanlagen, die Umweltbelastung des Betriebs, die schlechte Auftragslage und die hohe Exportabhängigkeit.
Die Produktion wurde daraufhin am 12. 11. 1986 eingestellt. Die 140 Belegschaftsangehörigen wurden arbeitslos. Sie hatten seit drei Monaten keine Löhne mehr erhalten. Der Konkursantrag wurde vom Amtsgericht abgelehnt. Nach einem Gutachten des Konkursverwalters Dr. Hahn beliefen sich die Verbindlichkeiten auf insgesamt vier Millionen DM. [27]
Anfang März 1987 wurde das Konkursverfahren endgültig mangels Masse eingestellt. Die Firma ist seit dem 29. 12. 1987 erloschen.[28]
Dekontaminierung und „Revitalisierung“ des Betriebsgeländes
Zwischen November 1995 und Februar 1996 fanden Bodenuntersuchungen auf dem früheren Betriebsgelände statt. Es stellte sich dabei heraus, dass das gesamte ehemalige Betriebsgelände nicht nur oberflächlich mit Arsen, Blei und Flusssäure kontaminiert war. Daraufhin wurde es eingezäunt und durfte nicht mehr betreten werden. Anwohner der Bollertstraße meldeten zur gleichen Zeit an mehreren Stellen den Austritt einer milchigen Flüssigkeit entlang der Straße. Bei Probebohrungen stellte sich heraus, dass es sich um Auswaschungen aus der mit Produktionsrückständen verunreinigten Salzhalde des früheren Kaliwerks und den behördlich genehmigten, offensichtlich nicht dichten, Schluckbrunnen für Schlämme und Flusssäure handelte. Das dadurch kontaminierte Grundwasser hatte sich seinen Weg durch das zerklüftete Gestein gebahnt. Der Landkreis Northeim empfahl den Bewohnern der belasteten Grundstücke, kein Obst und Gemüse aus eigenem Anbau mehr zu verzehren. Als erste Maßnahme wurden die Reste der Salzhalde abgedeckt. Im Mai 2002 errichtete die AWIA Göttingen im Auftrag des Landkreises Northeim unterhalb der früheren Glashütte an der B 241 eine Filtrierstation für 560 000 €. Diese sollte die aus sieben ehemaligen Schluckbrunnen immer noch austretende kontaminierte Flüssigkeit mit Hilfe von Pumpen auffangen und reinigen. Der Einsatz dieser Station war anfangs nur für einen begrenzten Zeitraum vorgesehen, doch immer wieder verlängert. Bis 2005 sind 40 000 Kubikmeter Flüssigkeit abgepumpt und dabei 30 t Fluoride ausgefiltert worden.
Im April 2005 begann man mit dem Abriss der ehemaligen Betriebsgebäude der Glashütte, verfüllte die Hohlräume und bedeckte sie mit einer dicken Schicht Mutterboden. Am 4. Mai 2005 wurde schließlich das früher weithin sichtbare Wahrzeichen der Glashütte Buder, der 60 m hohe Fabrikschornstein, gesprengt. [29]

Damit waren die Dekontaminierung und „Revitalisierung“ des ehemaligen Betriebsgeländes abgeschlossen.[30]
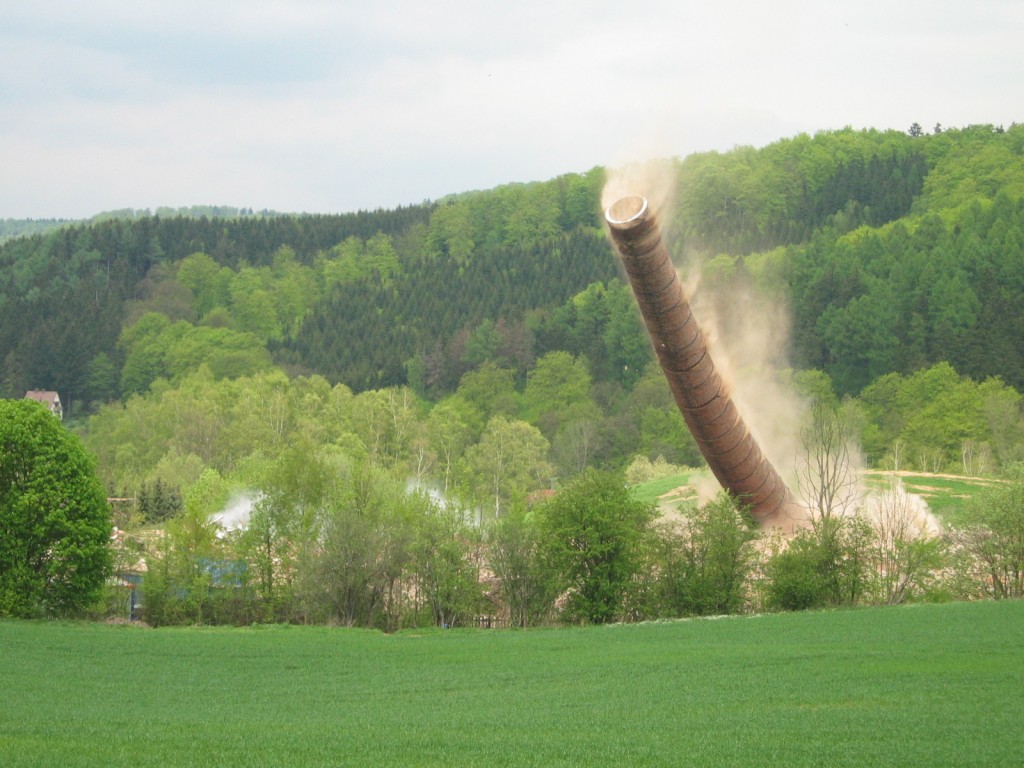
Quellenverzeichnis:
Literatur:
Buder Glashütte, Etwas über Glas, Manuskript, Volpriehausen 1975
Buder Crystal, Bleikristall in vielfältigen Variationen für einen breiten Käuferkreis, Manuskript Volpriehausen 1986
Buder Crystal, Bleikristall in vielfältigen Variationen für einen großen Käuferkreis, Werbeflyer Volpriehausen 1986.
Strietzel, Werner, Chronik der Firma Kristallglaswerk Buder in Volpriehausen, Manuskriptfragmen: Vorwort und Planung, Volpriehausen 2010
Ernst Buder Glashüttenwerke, Bahnbescheinigungsbuch Mai 1956 bis Mai 1957
Mitteilungen
H. Strietzel / H. Rückert, Volpriehausen
Ehemalige Buder- Mitarbeiter F. Baumer, K.H. Bolz, R. Raimann, Volpriehausen
Zeitungsartikel:
Sollinger Nachrichten (SN) und Sollinger Allgemeine (SA)
14.05.1963 – 20.08.1974 – 28. 11.1974 – 05.02.1975 – 16.07.1983 10.08.1983 – 22.09.1983 – 16.03.1984 – 21.09.1984 – 14. 11.1986 09.03.1987 – 14.11.2005 – 04.05.2005
[1] Strietzel, Chronik der Firma Kristallglaswerk Buder in Volpriehausen, Manuskript, S. 2
[2] Strietzel, Chronik, S. 3
[3] Buder Crystal, ,Bleikristall in vielfältigen Variationen, S. 1
[4] SN/S 5. 2. 1975
[5] Mitteilungen W. Strietzel / H. Rückert
[6] Bahnbescheinigungsbuch August 1956 bis Mai 1957
[7] Glashütte Buder, Etwas über Glas, Manuskript, S. 3/4
[8] Glashütte Buder, Etwas über Glas, S. 5/6
[9] Mitteilungen der ehemaliger Mitarbeiter F. Baumer, K.H. Bolz, R. Raimann
[10] Mitteilungen ehemaliger Mitarbeiter, s. o.
[11] Buder, Etwas über Glas, S. 5/6
[12] Mitteilungen F. Baumer, K.H. Bolz, R. Raimann
[13] SN/SA 14. 5.1963
[14] Mitteilungen F. Baumer
[15] SN/SA 20. 8. 1974
[16] SN/SA 20. 8. 1974
[17] SN/SA 28. 11. 1974
[18] SN/SA 20. 9. 1977
[19] SN/SA 10. 8. 1983
[20] Buder, Bleikristall in vielfältigen Variationen für einen großen Käuferkreis, S. 2
[21] SN/SA 16. 3. 1984
[22] SN/SA 16. 7. 1983
[23] Buder, Kristallglaswerk Buder, S. 3
[24] SN/SA 10.08.1983
[25] SN/SA 21.09.1984
[26] Mitteilungen: F. Baumer, K.H. Bolz, R. Raimann
[27] SN/SA 14.11.1986
[28] SN/SA 09.03.1987
[29] SA 04.05. 2005
[30] SA 14.11.2005